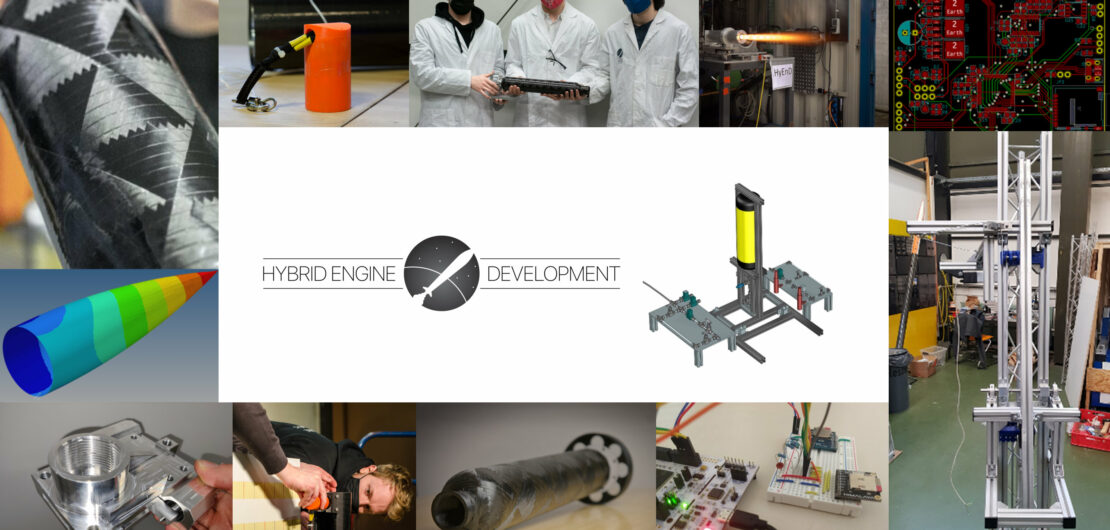
STERN 2 Project Update January 2021
We hope you all had a great start into 2021! For us, this is a great possibility to take a look back at 2020 and our achievements within the DLR STERN program. 2020 was the first full year of our second participation in the program, and despite the challenging situation we have made a lot of progress. Our subscale demonstrator rocket is taking shape with lots of prototyping going on, and we hope to launch it in a few months.
Structure and Aerodynamics:
Over the past year, the structure and aerodynamics team grew to a group of 17 members. With a lot of effort from everyone, we were able to achieve several milestones. Besides a range of manufactured prototypes we stepped up the simulations. A few of our milestones include:
The concept of the wound and etched oxidizer tank was applied to several prototypes. The now approved design will save up to 50 percent weight on our tank for the demonstrator rocket.
We now have an international team working on FEM and CFD simulations which are combined with CFRP testing and in-house development of epoxy resins. This enables us to optimize the structure aerodynamically and in terms of weight, so we can confident it will withstand upcoming loads and temperatures. The trajectory simulation became even more detailed and predicts impressive altitudes for N2ORTH.
Tests of different designs and approaches were also conducted for the nose cone, connectors, boat tail and other small parts around the rocket.
Propulsion:
Despite the challenging situation with the pandemic, the propulsion team was able to conduct a total of 25 successful hot fire tests with the subscale demonstrator engine HyFIVE in the time between September and December. The tests have shown that our in-house developed fuel enables smooth and stable combustion and our new composite ablative material works reliably. Also, different injector-types (showerhead, impingement, swirl) and nozzle designs have been evaluated.
Additionally, the team has constructed a 4-axis filament winding machine for the production of lightweight composite pressure vessels (combustion chambers, oxidizer tanks), nozzle components and rocket hull segments. First prototypes of the demonstrator engine have been produced for pressure tests in the new year, using one of our proprietary epoxy formulations with improved temperature- and fatigue properties.
Currently, further engine tests are postponed due to the high numbers of corona cases, but the propulsion team looks forward to even more tests with HyFIVE in the future.
Fluid System:
2020 has certainly been an exciting year for the fluid system team. We made detailed designs for the concepts developed in 2019. Hence, our main work was the design and testing of various prototypes. In particular, the prototypes for the emergency release valve and the main valves of both the demonstrator and N2ORTH rocket yielded promising results. While testing continues, we are using the gathered knowledge for the design of the flight versions of the individual components.
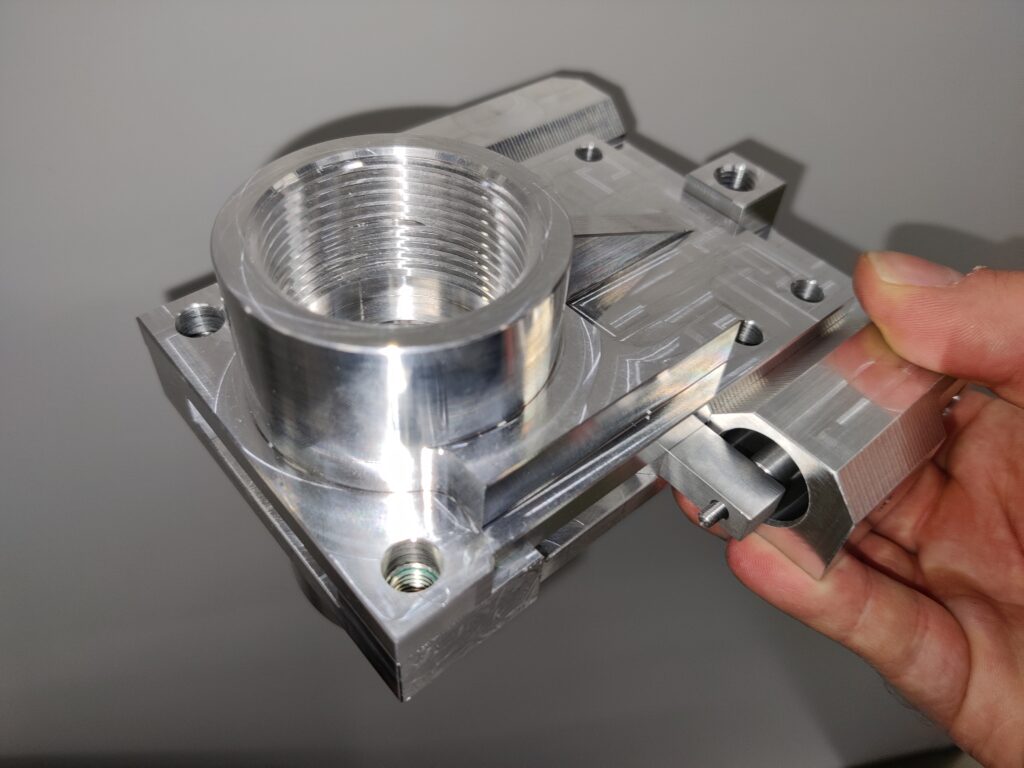
Recovery:
Over the past year, the recovery team has had several successes. While there were only concepts, at the beginning of the year, there have already been the first successful tests and many improvements have already been incorporated into the existing concept.
The first pyro tests with our mortar-like ejection system could already take place in October. In November, we have tested the ejection of the drogue parachute. A prototype of the entire recovery bay has already been built and will be tested in a drop test at the beginning of the new year.
There is still a lot of work ahead of us and many more components to test, nonetheless the results so far make us confident of a successful recovery of the rockets.
Avionics:
We were able to achieve nearly all goals set for this year. We decided onto a final system topology, allowing us to spend all our time onto the individual modules. A major part of our work this year was to select and test components to fulfill every given task like recording the flight trajectory, measuring performance data of the engine as well as transmitting the collected data to the ground station. With the component selection nearly done we are now looking forward to designing and building the flight versions of the demonstrator rocket, which then need to be firmly tested to ensure smooth operation of all modules working together for the launch.
Ground Support Equipment:
In the last year, we have made a lot of progress in the GSE subsystem. We assembled the launch pad which will be used for the demonstrator launch. The arm mechanism, which enables us to undock the fuel interface remotely, is currently being assembled as well.
Progress was also made in our electronic department. It completed development of the system used to control and monitor the fueling process, as well as all other functions of the launch platform. It is also used to schedule and fire all pyrotechnic devices used to light the engine at launch.
The control system was split into three different custom-made PCBs and is managed using a Raspberry Pi running C Code. The graphical user interface running remotely in the control room is currently under development and will allow for easy monitoring and actuation of all functions.
The fueling system has evolved as well. It is planned to use a diving bottle as a buffer tank to fill the demonstrator rocket with oxidizer. The process uses a series of solenoid valves and sensors to ensure the right oxidizer level and pressure in the main tank while also being remotely actuated. In the next couple of months till the launch of the demonstrator rocket, there will be a complete dry run of the entire fueling process in conjunction with the fluid system.
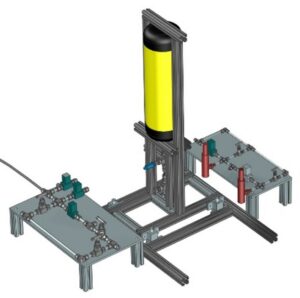