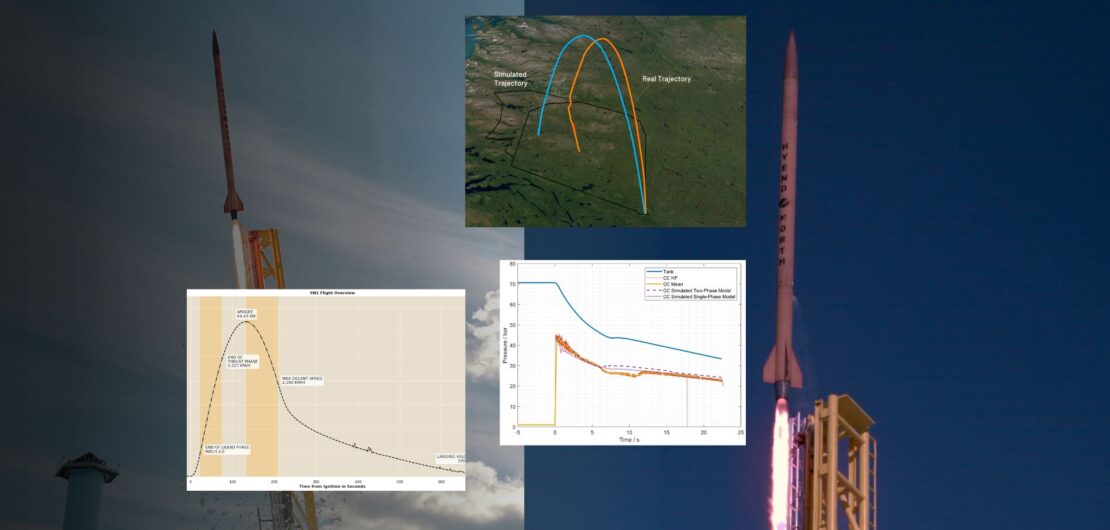
First Results of the N₂ORTH Post Flight Analysis
Since our N2ORTH Launch Campaign in April, some time has passed, and the team took a well-deserved break. Nevertheless, we had our Post Flight Analysis Review in Bonn at the beginning of June, and we want to share some of the results with you.
Analysis of the 1st Launch:
The first launch took place on Tuesday, April 18. Originally scheduled for Monday, the launch was postponed to Tuesday in order to double check the avionics and launcher interfaces.
The countdown began at 06:15 and went very smoothly. There was a short pause to complete the transfer of nitrous oxide from the intermediate tanks to the rocket tank. This delay was caused by the fact that the boxing of the rocket itself was less insulated than expected. To compensate, the nitrous oxide in the intermediate tanks was heated to a higher temperature. The final oxidizer mass in the rocket was 95 kg and the launch elevation was set at 81.4°.
The launch at 11:05 local time went smoothly without any problems. The rocket reached a maximum speed of Mach 3 / 3,150 km/h after about 20 seconds. The engine provided thrust for about 75 seconds, with a transition to the gas phase after 18 seconds. This data was obtained from the IMU as the lower data acquisition system suffered a cable disconnect at liftoff. This means there is no tank and chamber pressure data for the flight. However, the upper data acquisition system continued to operate and a maximum tip temperature of 240°C was reached.
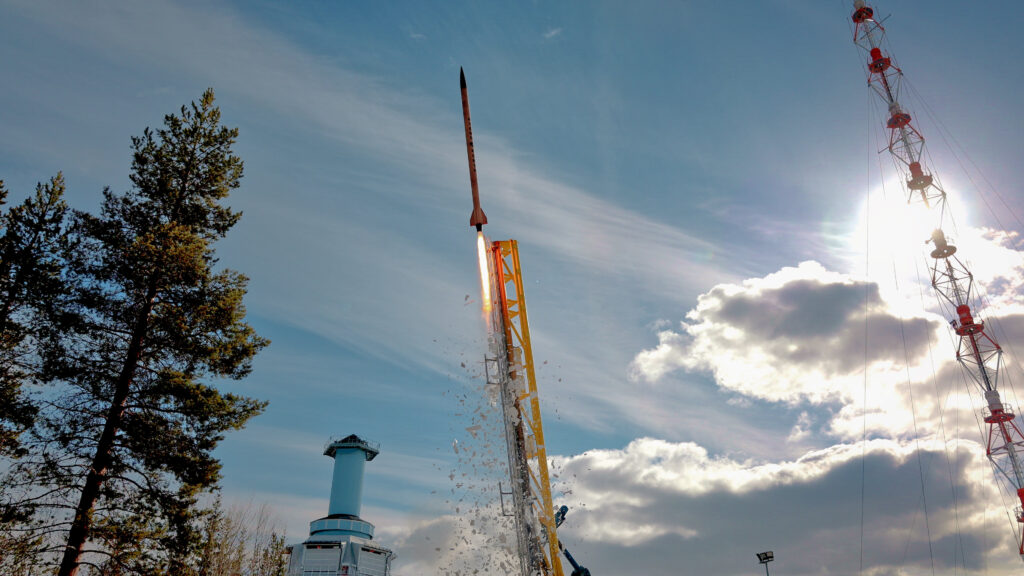
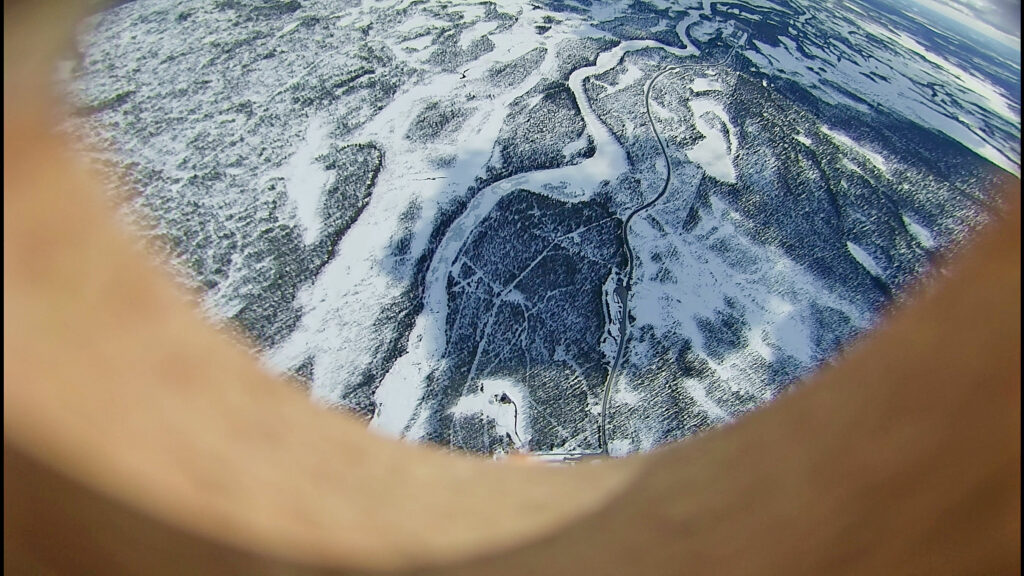
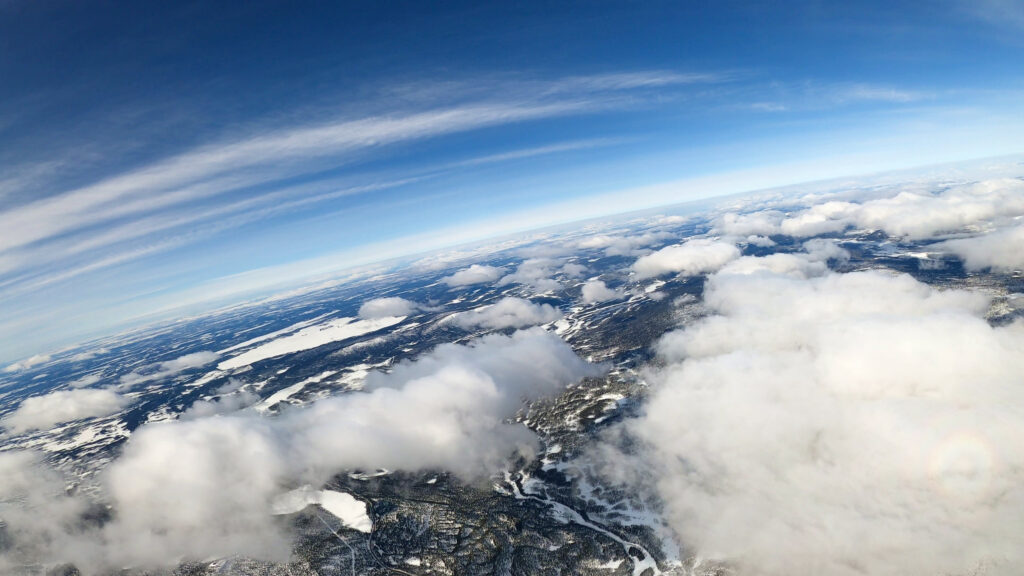
Apogee was reached at an altitude of 64.4 km after 132 s. This was only a 0.2% difference to the predicted apogee by the simulation. However, the drogue parachute deployment was triggered 9 s earlier by the Telemegas. The drogue deployed without problems at Mach 0.9-1. However, reviewing the onboard video, it can be seen that the main parachute’s three-ring release system was already activated. Up to this point, the main chute was still held in place by two straps in the recovery section, as the drag generated by the drogue was not sufficient to pull it out. However, during the descent the drag increased until the main parachute was released at an altitude of 36 km and a speed of Mach 1.8. Since the main parachute is not designed for these conditions, it was immediately detached from the rocket together with the drogue parachute.
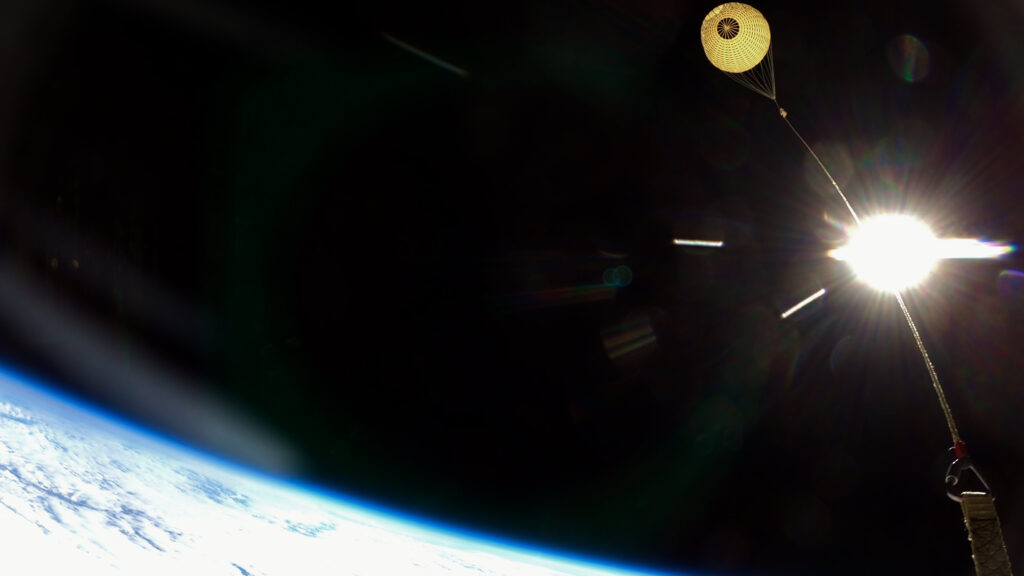
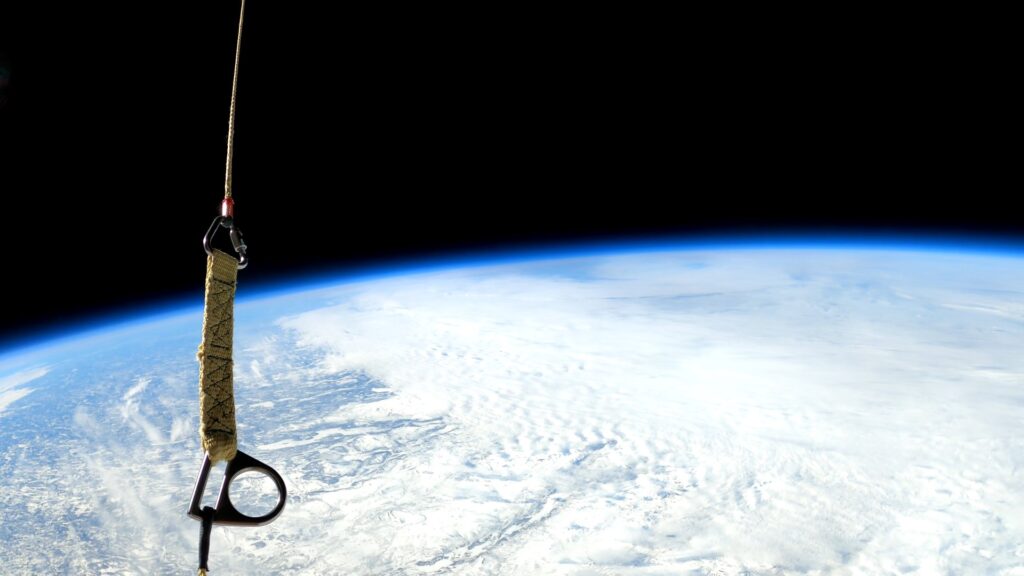
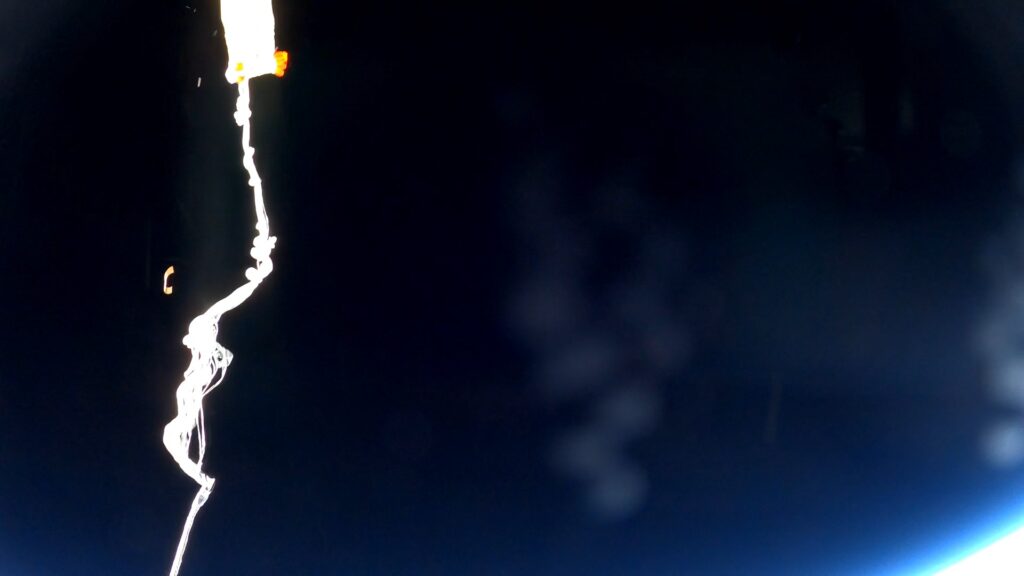
The rocket then went into a tumble mode with a high spin rate, which helped to keep the descent rate relatively low. The avionics were able to continue transmitting the position up to an altitude of 1.3 km. At this point, the line of sight prevented further data transmission. Thanks to the precise position (downrange: 48 km), the rocket was easily located and recovered by helicopter only 3 hours after launch.
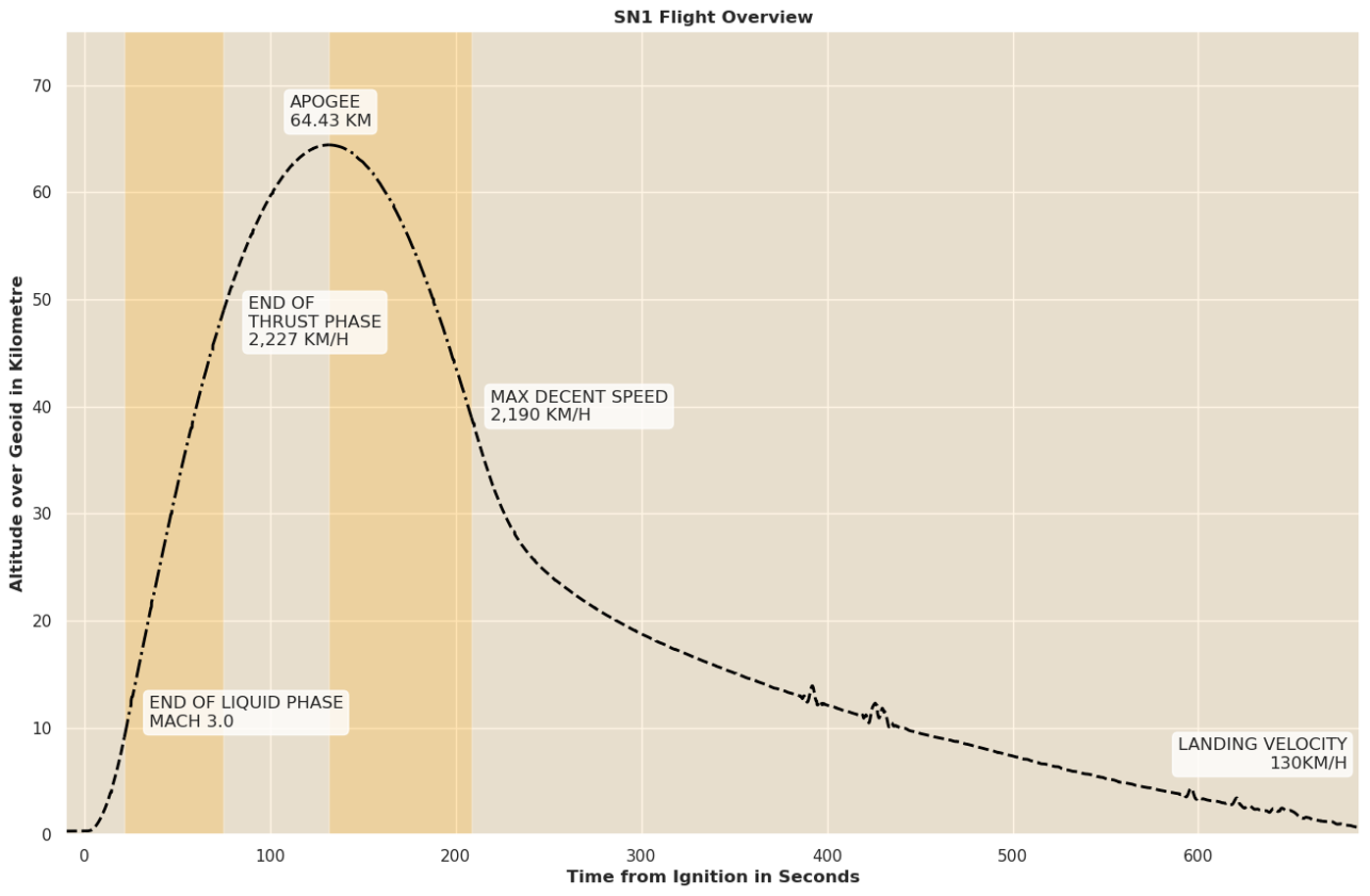
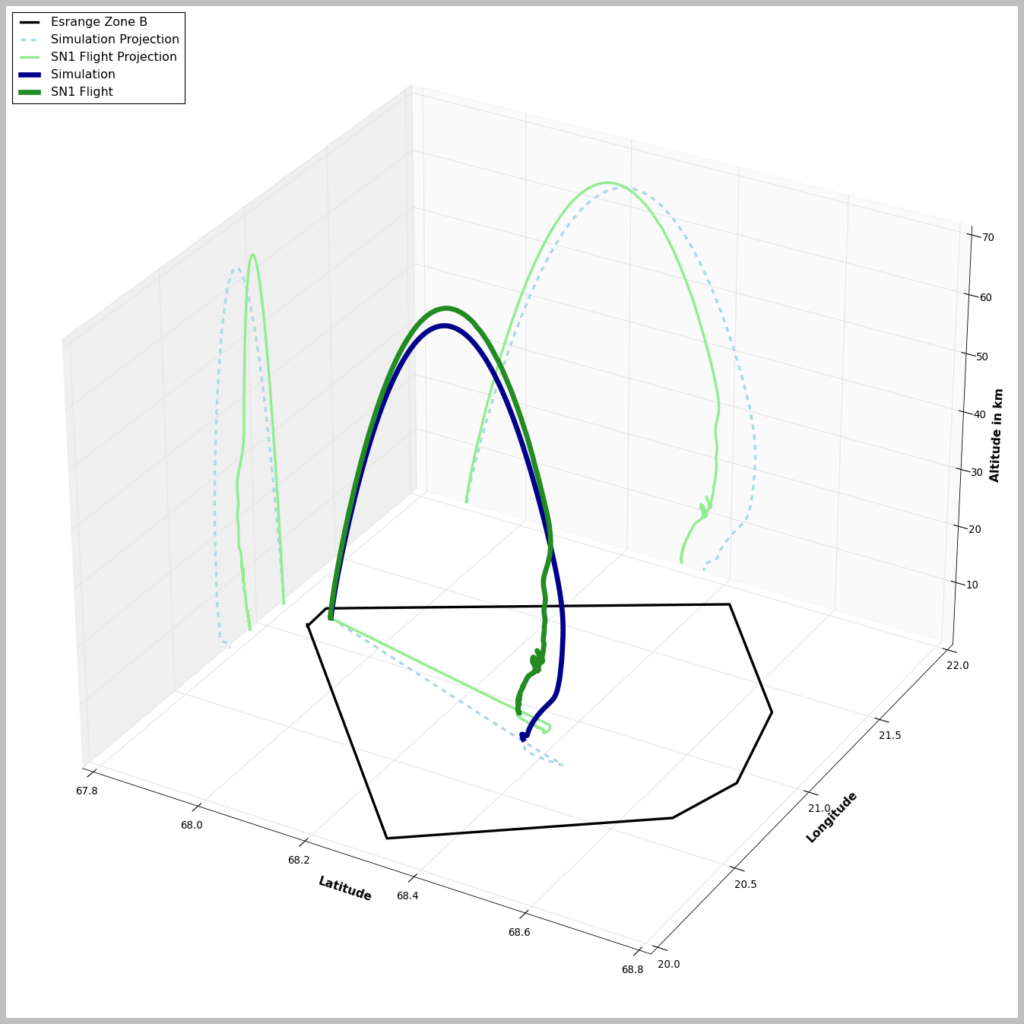
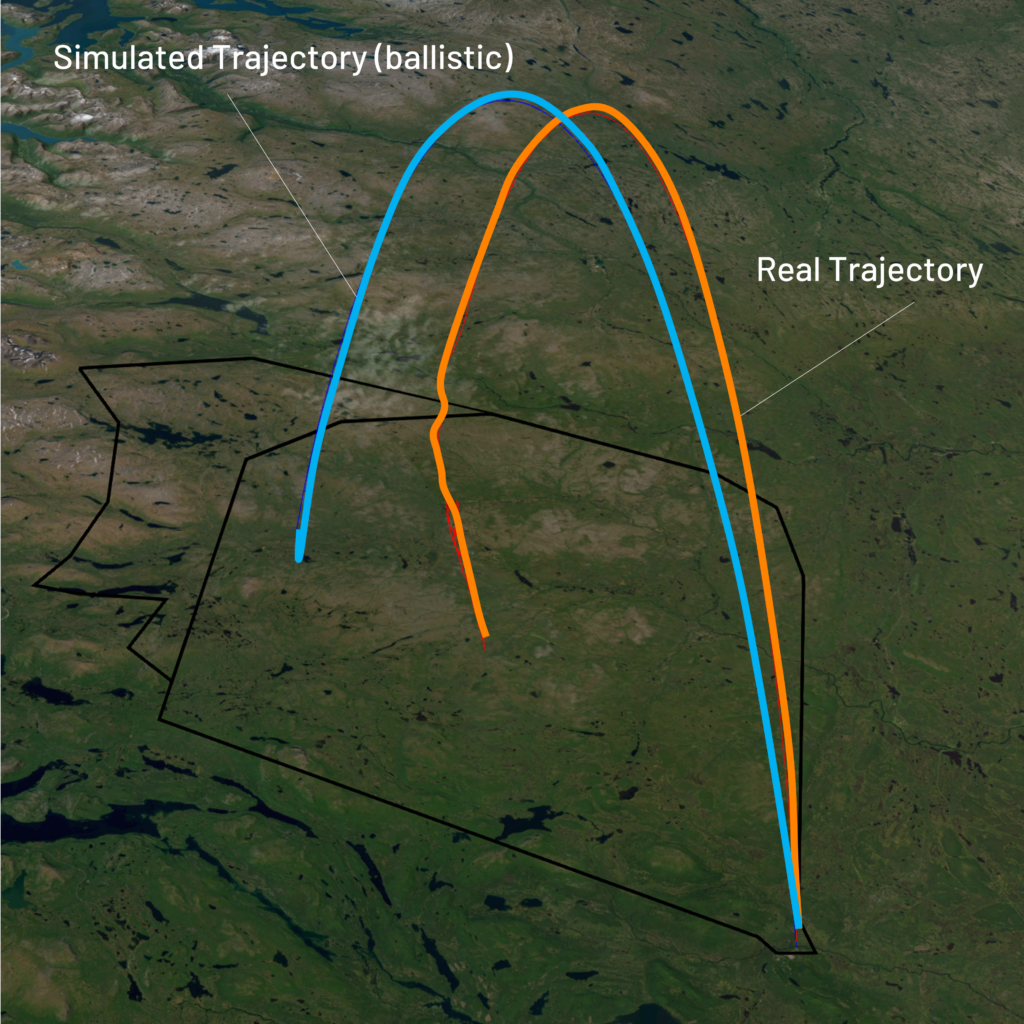
A review of the onboard data showed that the rocket landed at a vertical speed of 36 m/s. The avionics were internally damaged due to the non-nominal recovery sequence and landing speed, but all data could be recovered. Also, the recovery section and one of the fins suffered some structural damage.
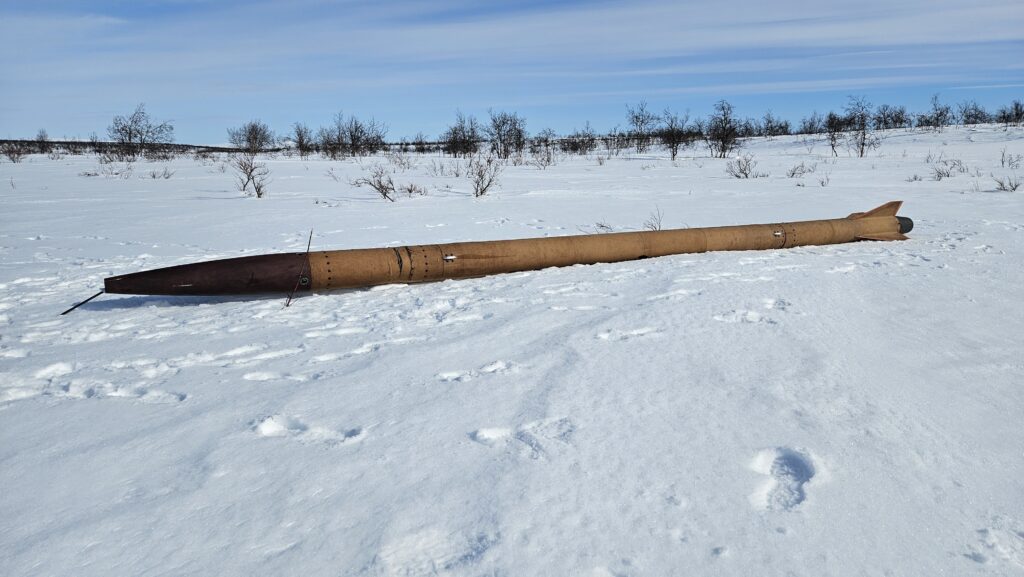
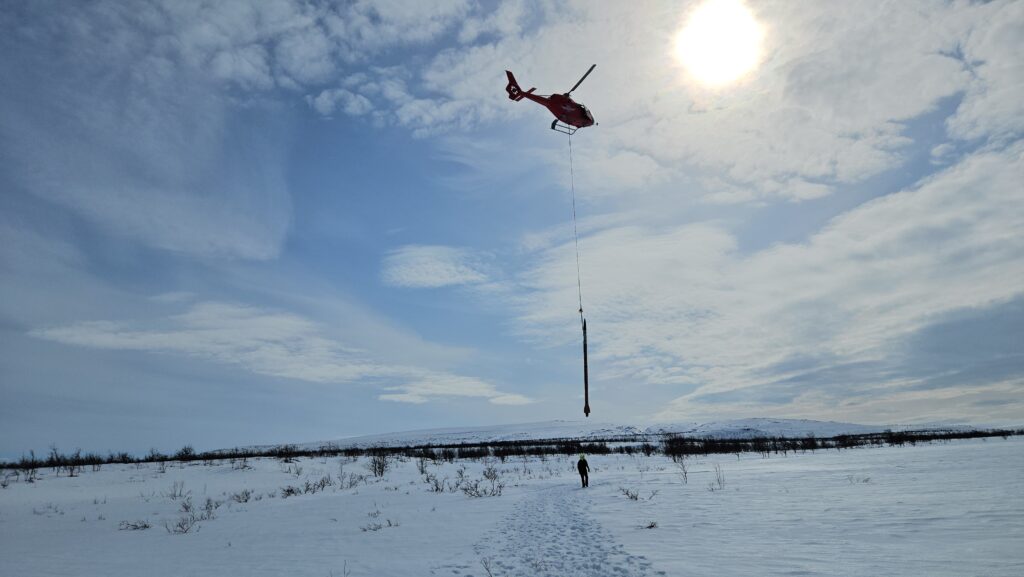
The reason for the non-nominal recovery sequence was found during investigations on the following day and was traced to a misconfiguration in the Telemega software. As the cause was quickly found, HyEnD was able to ensure that the second launch would not have the same problem and continued preparations for the second launch.
Analysis of the 2nd Launch:
Having demonstrated with the first launch that our simulations are capable of predicting the rocket’s trajectory with high accuracy, and having quickly identified the cause of the non-nominal recovery sequence, the team decided to continue preparations for the launch of the second rocket.
Unlike the first rocket, the second N2ORTH rocket has a linerless Type V pressure vessel with an ETFE coating on the inside to ensure compatibility with nitrous oxide. The elimination of the aluminum liner reduces the dry mass of the rocket by 7.7 kg (10%). In addition, the Esrange safety and operations team approved an increase in the launch rail elevation. It was decided to target an oxidizer mass of 105 kg for the second rocket, which would result in a >90% chance of reaching an altitude of more than 100 km and thus the Kármán line. A higher oxidizer mass would have been technically possible, but would have resulted in the rocket landing outside the designated landing zone.
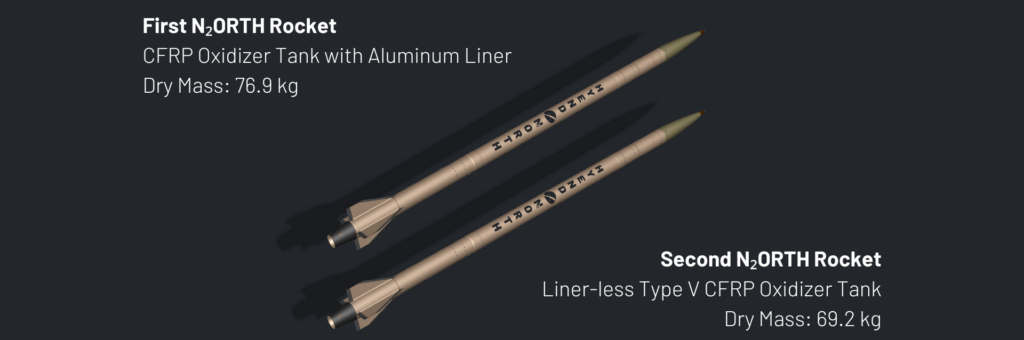
The launch attempt took place on Monday, April 24. The Styrofoam box of the rocket was improved in order that the launch team could easily control the temperature and keep it within the desired range. However, during the oxidizer loading process, the solenoid valve in the rocket could not be activated. It was decided to continue the countdown with an adjusted oxidizer loading procedure. With the modified procedure, the target oxidizer mass, temperature, and pressure were achieved with another short countdown pause. However, the nitrogen content of the oxidizer tank filling was higher than originally simulated.
At 14:10 local time, the rocket launched with an elevation of 82.2°. Unfortunately, the rocket encountered an anomaly that caused it to break up 22.4 seconds after liftoff. At this point, the rocket was at an altitude of 11 km, traveling at Mach 3, and still in sight of the team members and cameras on the radar hill. Due to the anomaly, the rocket disintegrated into several pieces. The avionics were able to send data to the ground station until this point. The timing of the anomaly is interesting because both the transition from liquid to gaseous nitrous oxide and the maximum dynamic pressure occur at this time.
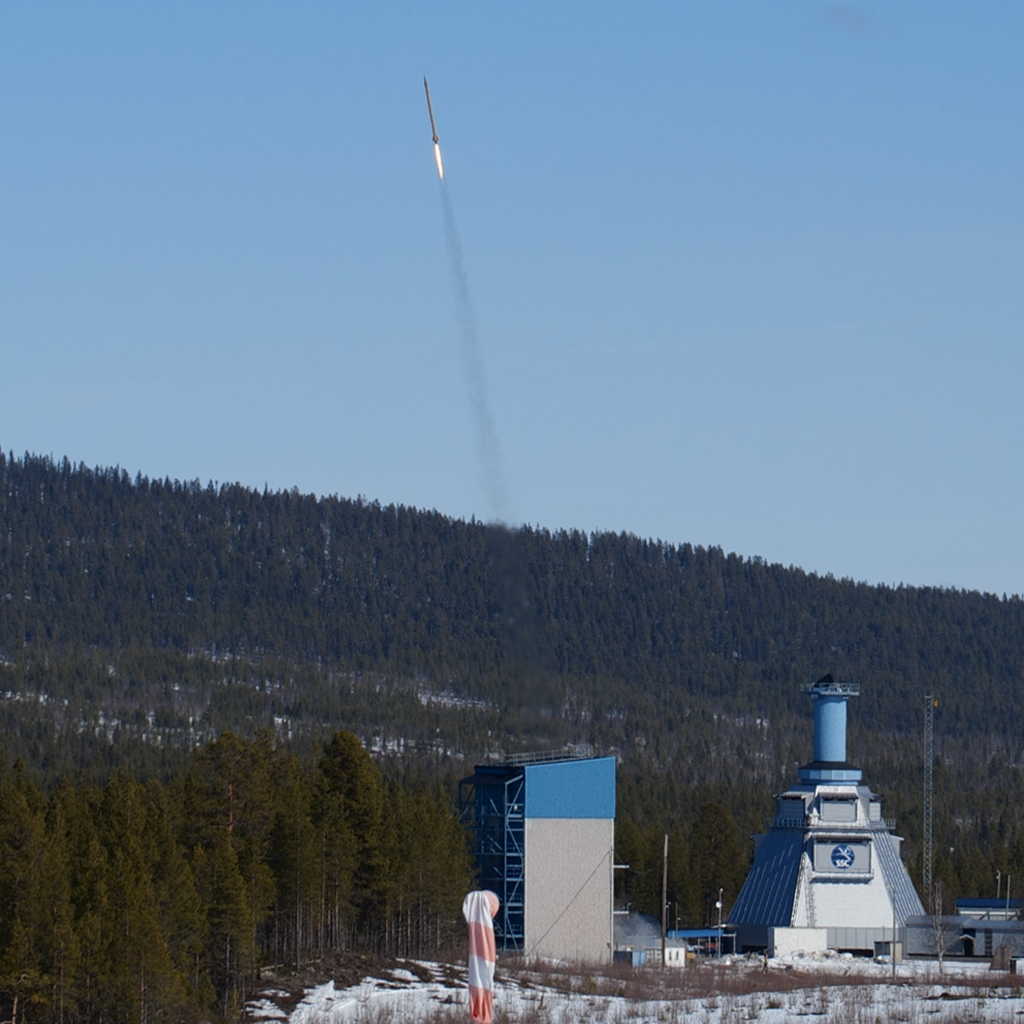
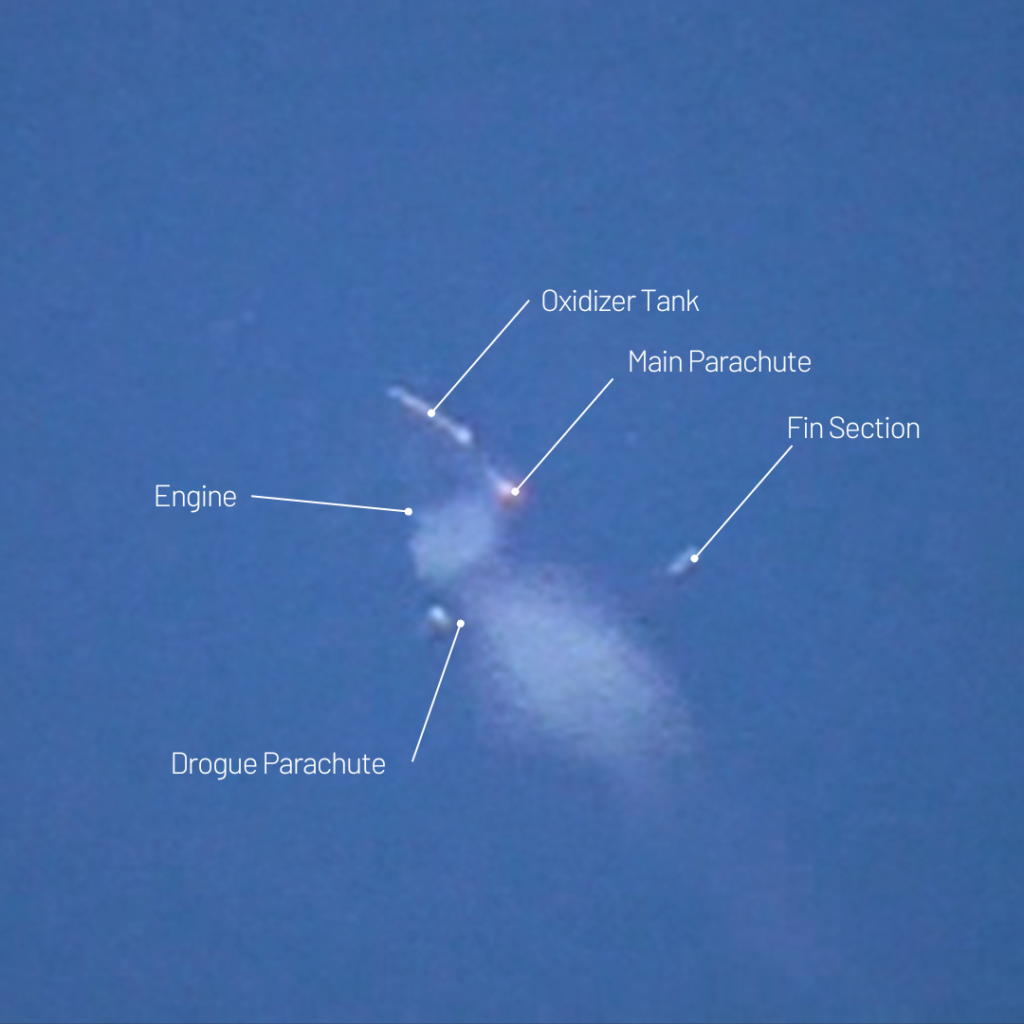
One of the cameras mounted on a theodolite was able to follow the oxidizer tank until it hit the ground. The video and azimuth information allowed the Esrange team to retrieve the tank by snowmobile the next day. The tank and its attached fluid system components were undamaged except for the broken interfaces at both ends. Fortunately, the Rocket Status Measurement System (RSMS) SD card attached to the oxidizer tank was still intact, giving the team access to high frequency (14 kS/s) chamber pressure data.
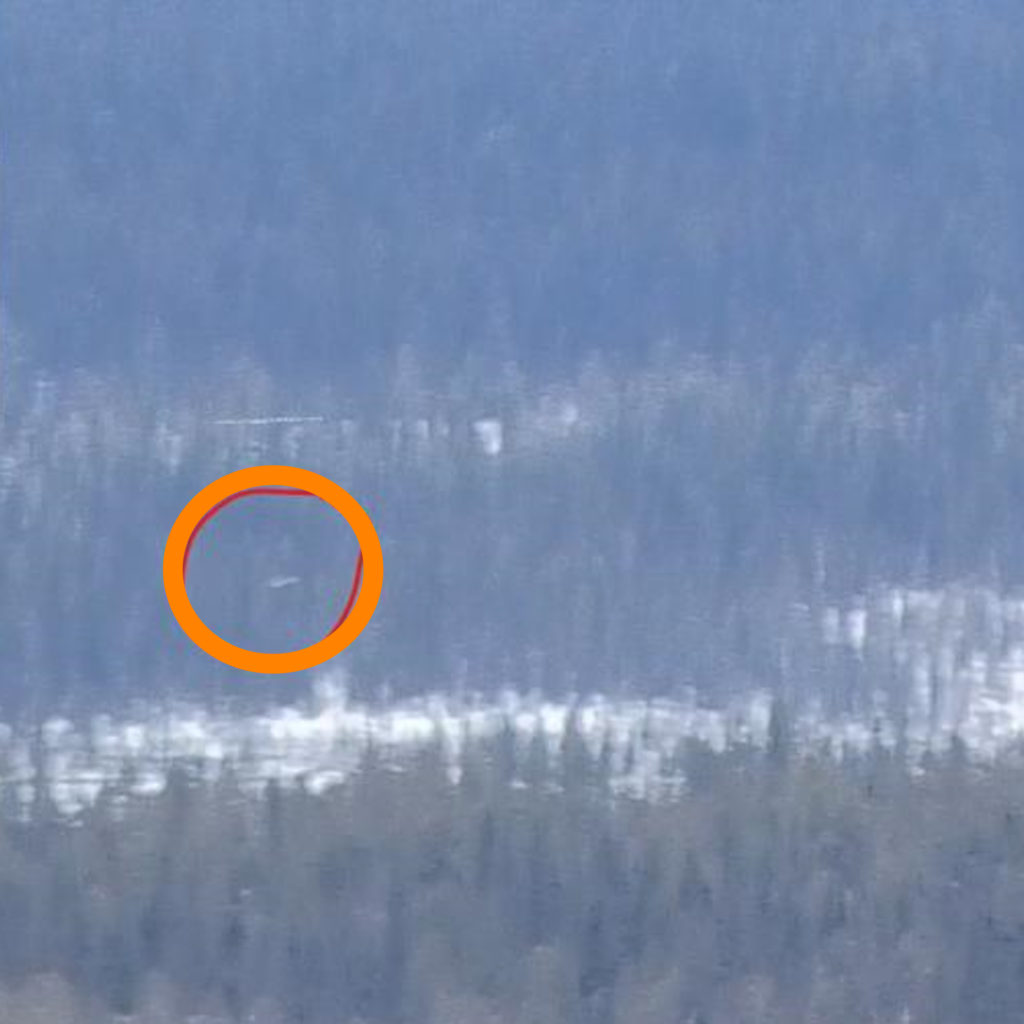
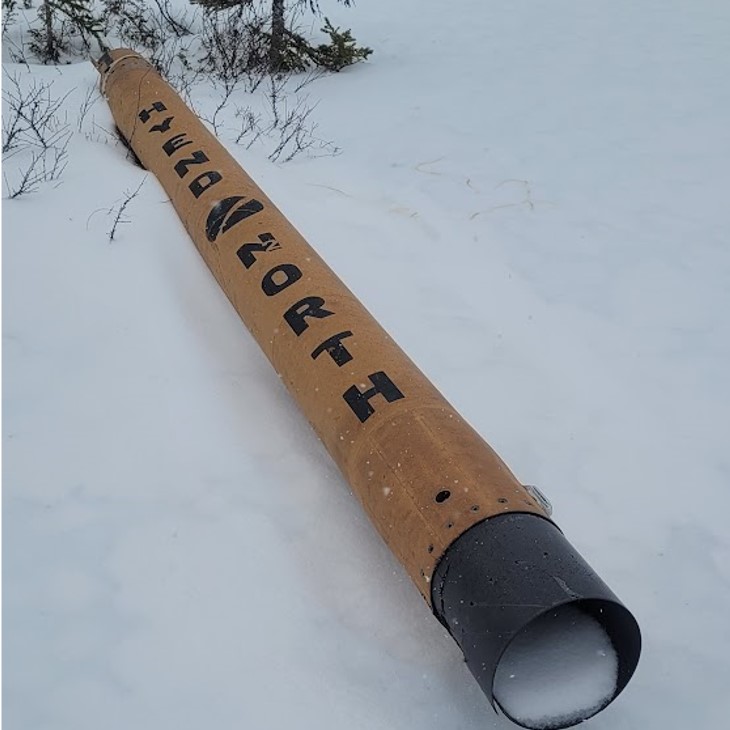
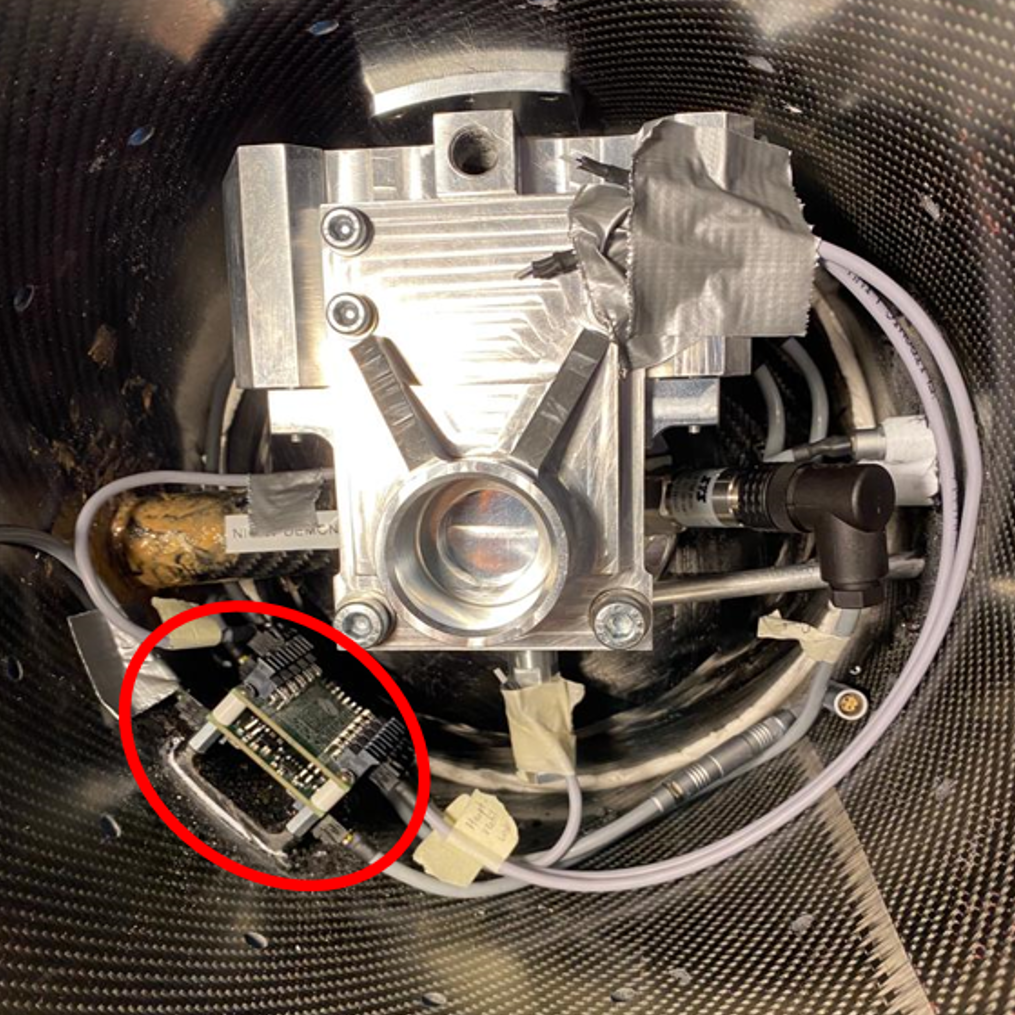
A review of the cameras on the launcher revealed that the oxidizer release valve was opened at launch, resulting in a slow (<100 g/s) release of liquid nitrous oxide to the side of the rocket. Inspection of the valve (which was still attached to the recovered oxidizer tank) revealed that the pyro charge within the valve was not activated, indicating that the opening was triggered by a shock load at launch. The influence of the vented nitrous oxide on the rockets aerodynamics is still under investigation.
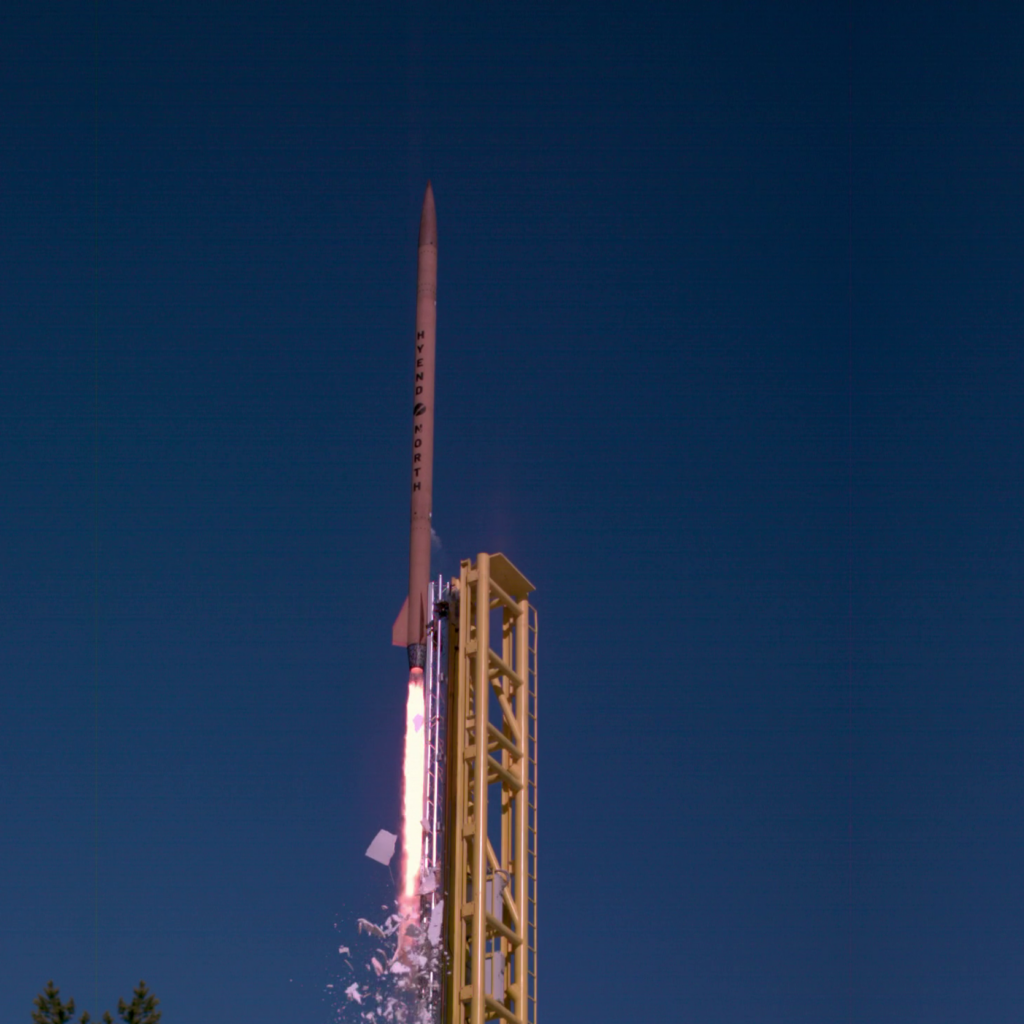
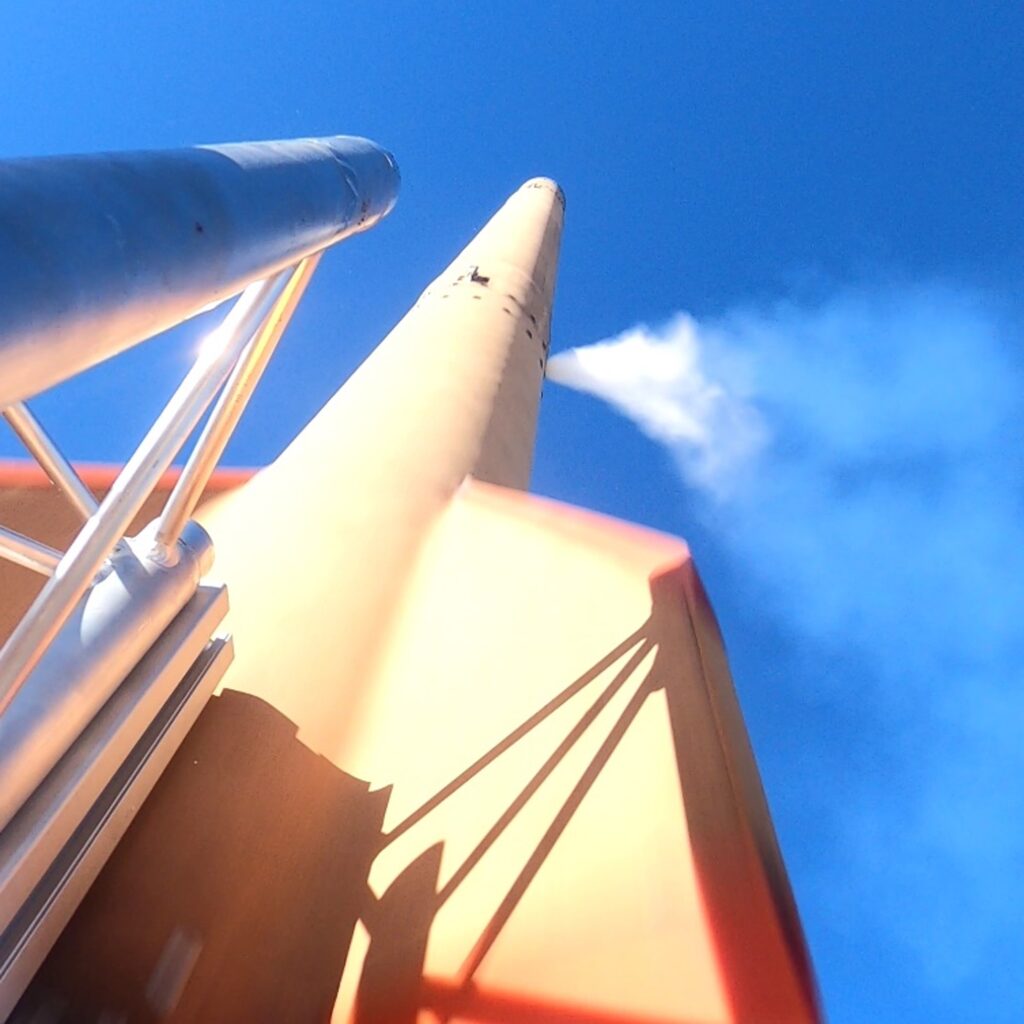
Chamber pressure data shows no indication of engine malfunction until a loss of chamber pressure occurs at 22.4 s, which is associated with the breakup of the rocket. The IMU data shows a continuous increase in lateral acceleration from 0 to 2.5 g beginning at 20 s, with a rapid increase to more than 15 g at break-up. Since the later acceleration begins to increase to a point where the combustion chamber pressure is nominal, a failure of the propulsion system is unlikely. The IMU data also shows a low spin rate of less than 0.52 Hz and no evidence of pitch-roll coupling.
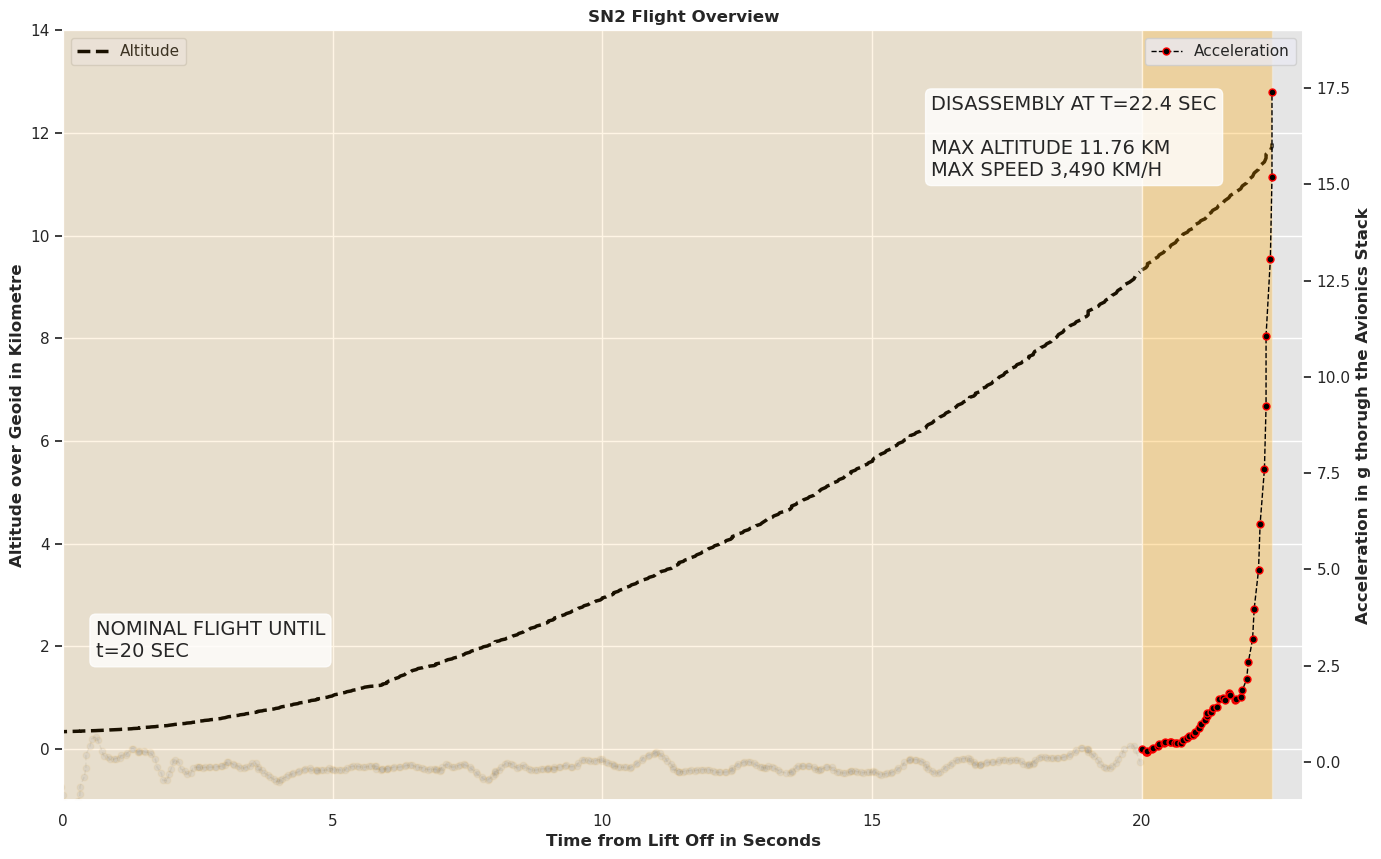
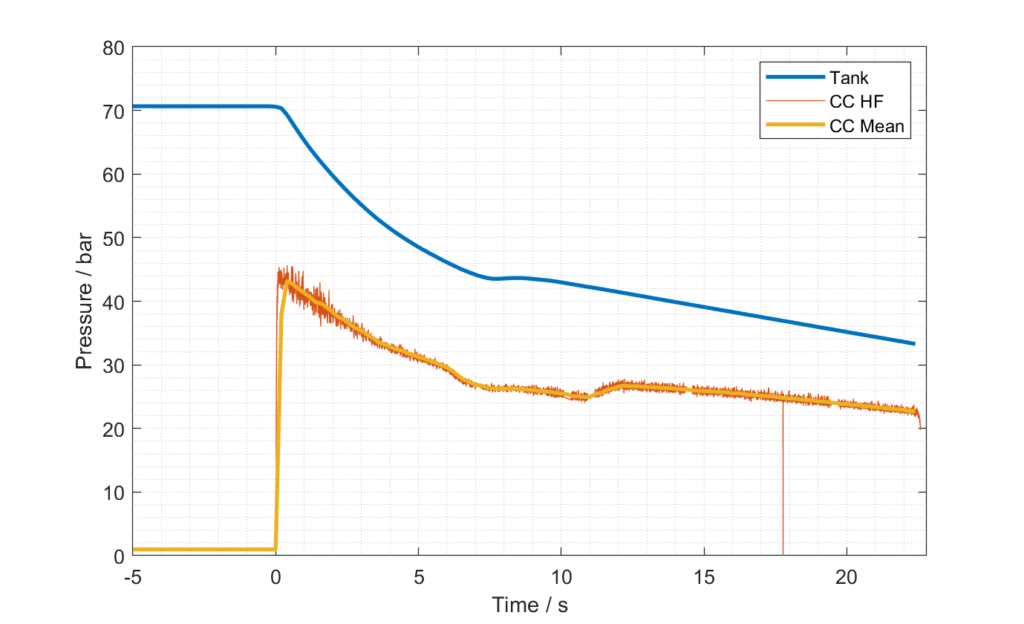
Based on the available data, the final cause of the failure cannot be clearly identified. However, the possibility remains that other components of the rocket will be found by the SSC team in the future. At this point, it can be concluded that the breakup of the rocket was the result of either a structural failure during launch, an unexpected aerodynamic load on the rocket, or a combination of both effects.
Nevertheless, HyEnD is very proud of what has been achieved with the launch campaign – setting new records and pushing the limits of (student) hybrid propulsion. The two weeks in Sweden were an amazing time – thanks to a great team, good logistics and organization as well as the cooperation with DLR and SSC.